This website uses cookies so that we can provide you with the best user experience possible. Cookie information is stored in your browser and performs functions such as recognising you when you return to our website and helping our team to understand which sections of the website you find most interesting and useful.
Month: October 2023
Supply Chain Considerations for Plastics
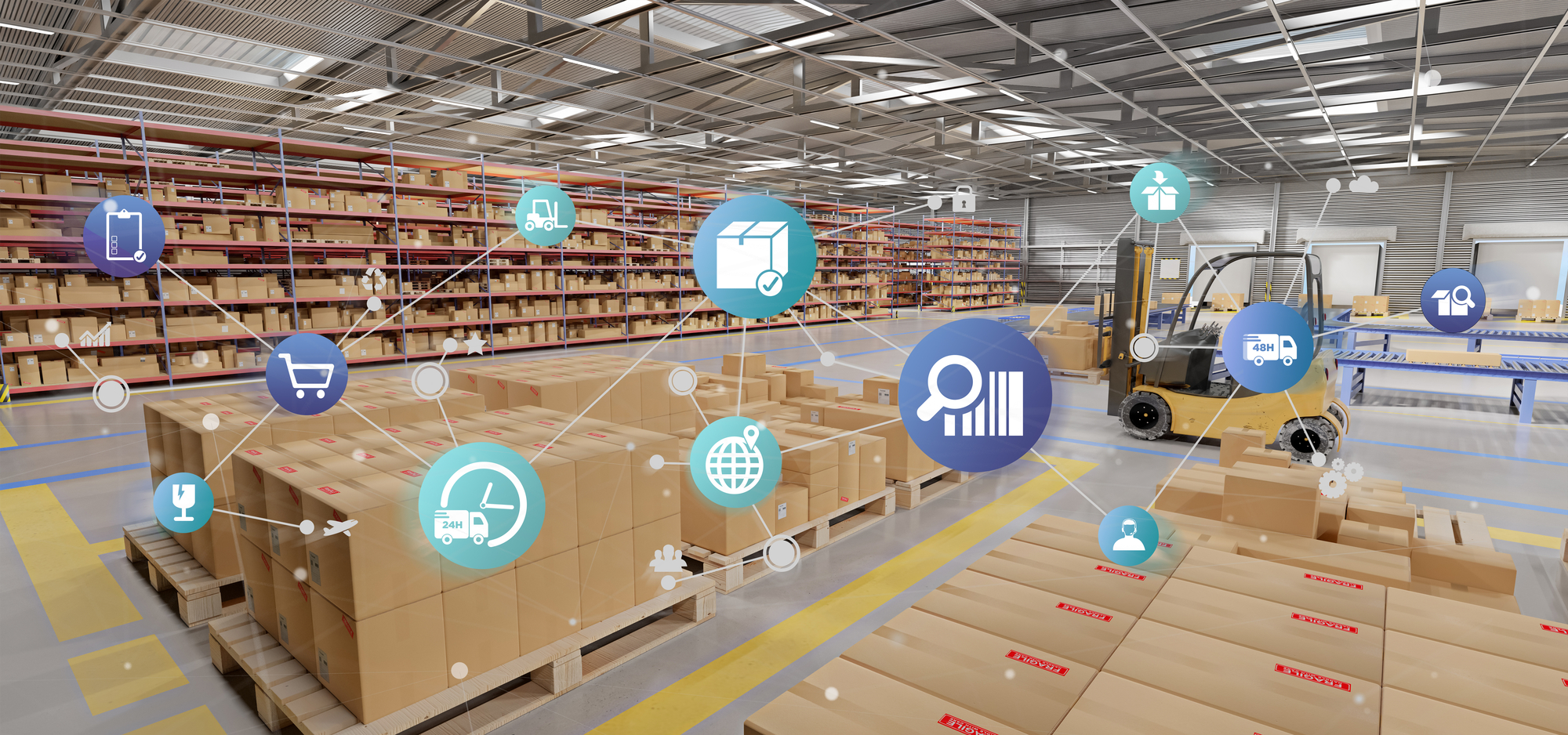
Supply chain productivity is critical in injection molding processes where even small delays can lead to costly and time-consuming problems. To ensure that injection molded plastics are delivered on time and in the best possible quality, a business should invest in optimizing their supply chain. Here are some tips to maximize supply chain productivity for injection molding plastics:
Full Service Manufacturing Versus Not
Full-service manufacturing is a great way for businesses to get the most out of their production process. From the smallest of projects to the largest, full-service manufacturers offer a wide range of services that are designed to help businesses achieve greater efficiency and cost savings. Let’s take a look at some of the top benefits of full-service manufacturing compared to other alternatives.
1. High Quality Production: Full-service manufacturers provide customers with a high level of craftsmanship and consistent quality products. This includes customizing parts and processes according to exact specifications, meaning that businesses can be confident that the end result will be exactly as intended.
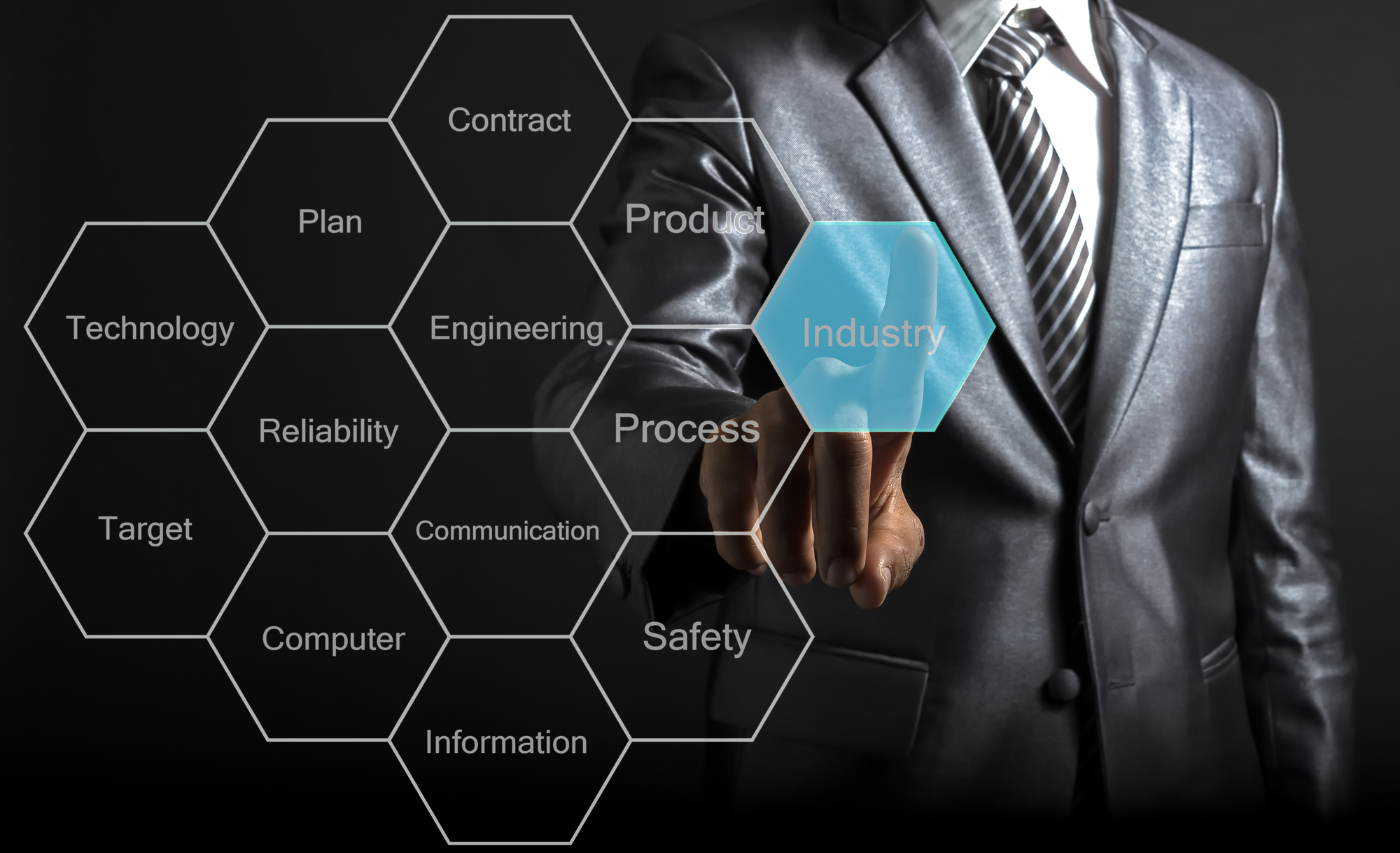
Replacing Metal Parts with High-Performance Plastics
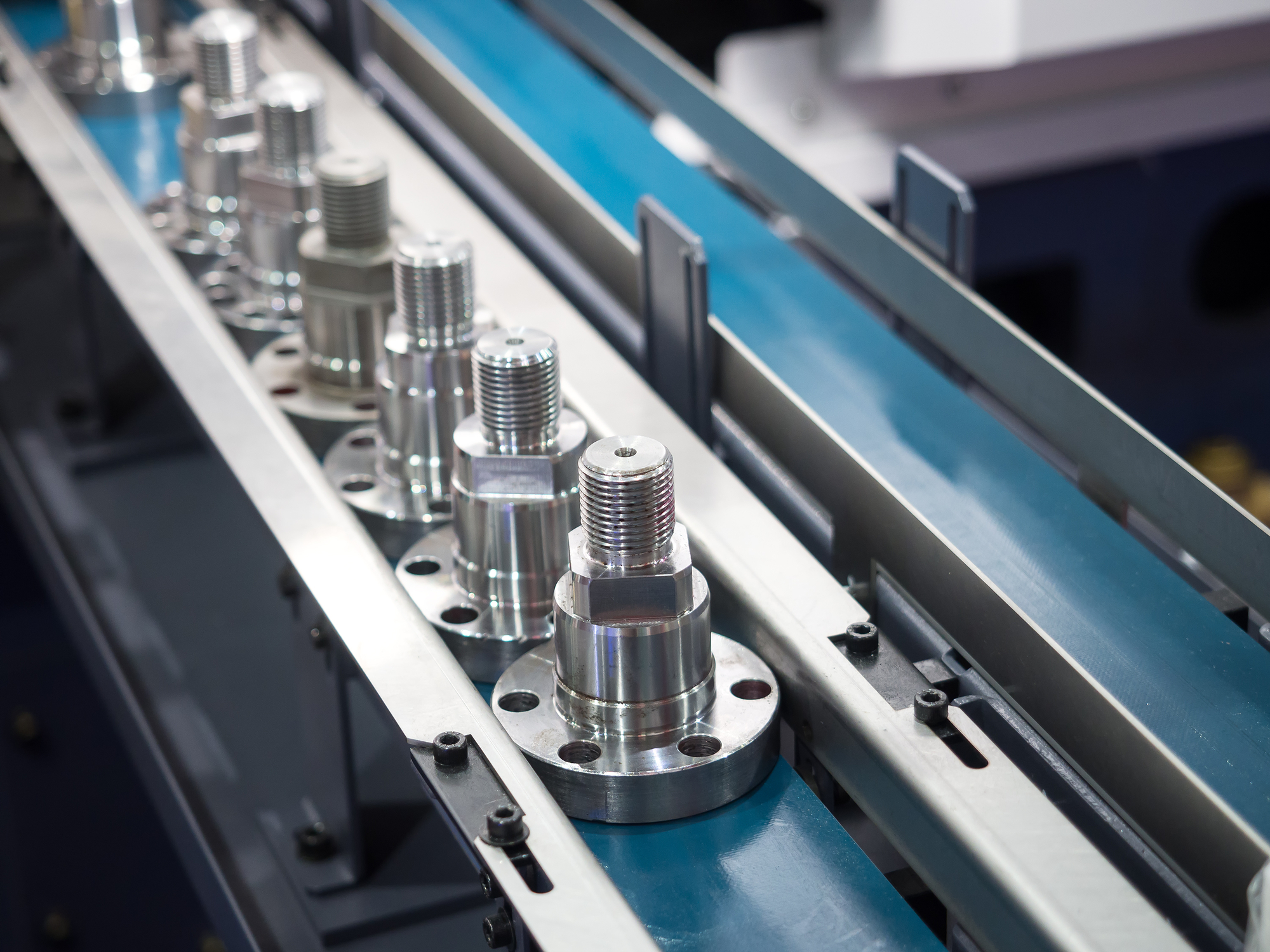
In recent years, plastic materials have become increasingly popular when it comes to replacing traditional metal parts. Plastic materials offer a variety of benefits, including their light weight, affordability, and corrosion resistance. They are also easy to machined and can be designed in ways that metal parts can’t. In this blog post, we’ll discuss the benefits of replacing metal parts with high performance plastics for various industrial applications.
1. Low Weight: One of the major advantages of replacing metal parts with high performance plastic materials is the low weight of these components. This makes them easier to transport and also reduces production costs as less material is needed.
2. High Strength: Plastics can be manufactured to provide high levels of strength and durability even when compared to many metals. This means that they can be used in manufacturing high-end products that require superior strength and performance.
3. Durability: Plastic components offer superior resistance to chemical and environmental exposure when compared to traditional metal parts. This means that products manufactured with plastic components will last much longer than their metal counterparts.
4. Corrosion-Resistance: Plastics are inherently corrosion-resistant, which makes them a great option for applications where this is a big concern. This can also reduce the need for any protective coatings and make it easier to maintain the part.
5. Cost-Effective: Plastic materials can be manufactured at a much lower cost than traditional metal parts, which can greatly reduce the total cost of a product or project. This is especially beneficial for large-scale production runs where the cost of materials can become a major factor.
Replacing metal parts with high performance plastic materials offers a wide range of benefits, including lower costs and improved performance. By selecting the right material and working with skilled professionals, businesses can ensure that their products work as intended while also reducing production costs.
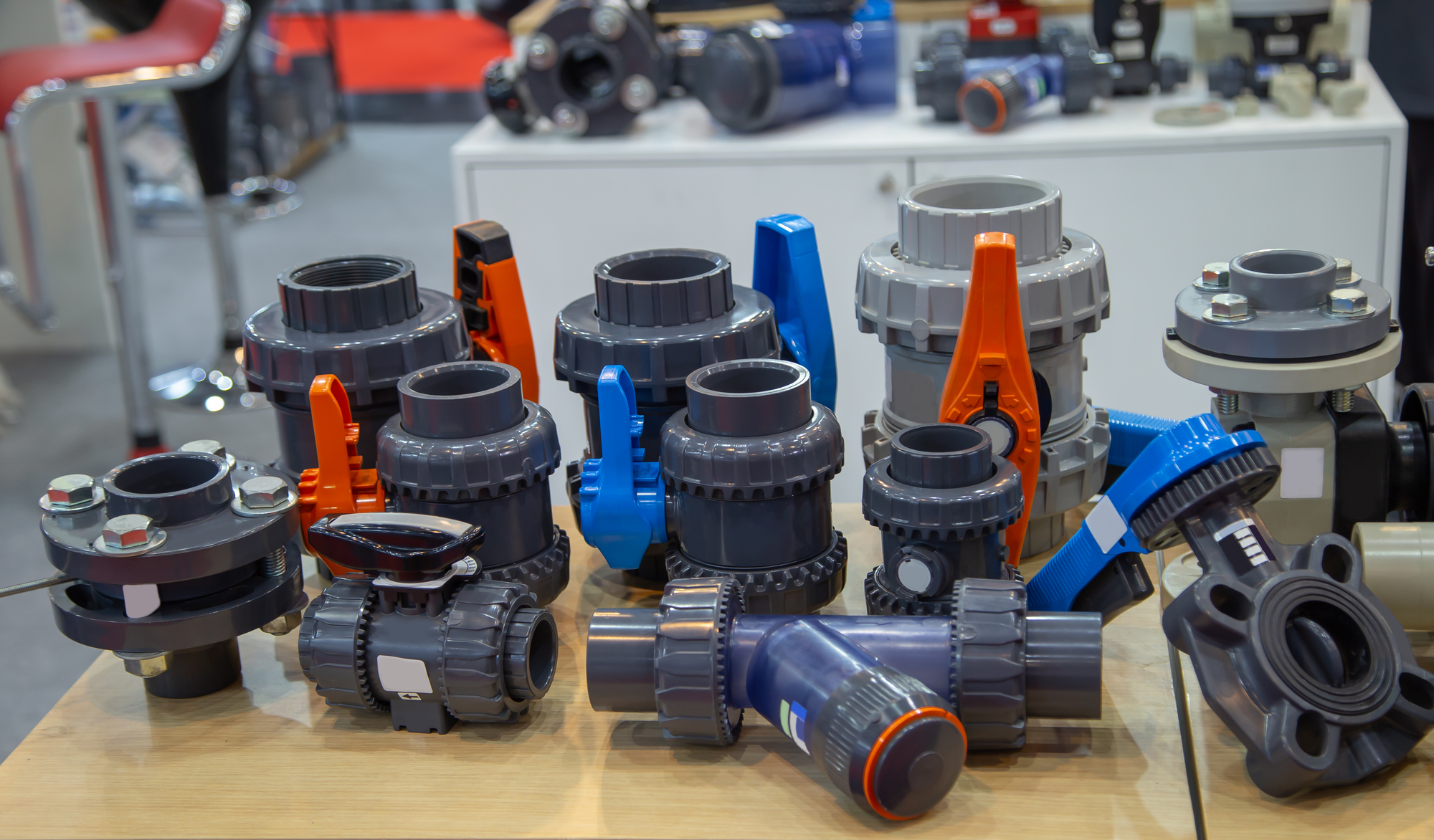